For the correct understanding of the methodology of updating and implementing the supply chain strategy, we will initially make a brief presentation of the methodology’s stages:
The stages of establishing the supply chain strategy
Stages 1 and 2

Effective planning of a supply chain strategy begins with the process of knowing the company’s business and departmental strategies in stages 1 & 2.
A company’s internal processes are cross-functional, their activities being carried out by various departmental structures focused on achieving their own objectives.
Compromises at the functional, departmental and company level, between what is desired and what is practically possible, cannot be done rationally, without the most complete understanding of reality: customer requirements, product portfolio, market segments, competitor profile and best practices specific to the industry, multifunctional strengths and weaknesses of the company, external alliances and partnerships, sales channels, operational IT capabilities, types of risks, etc.
In conclusion, it is ineffective to plan the supply chain strategy independently of the business strategy and the departmental strategies, because, as often happens, key organizational functions, such as marketing-sales, IT or production, are decisive in establishing business objectives and correct implementation of the company’s strategy.
Stages 3, 4 and 5
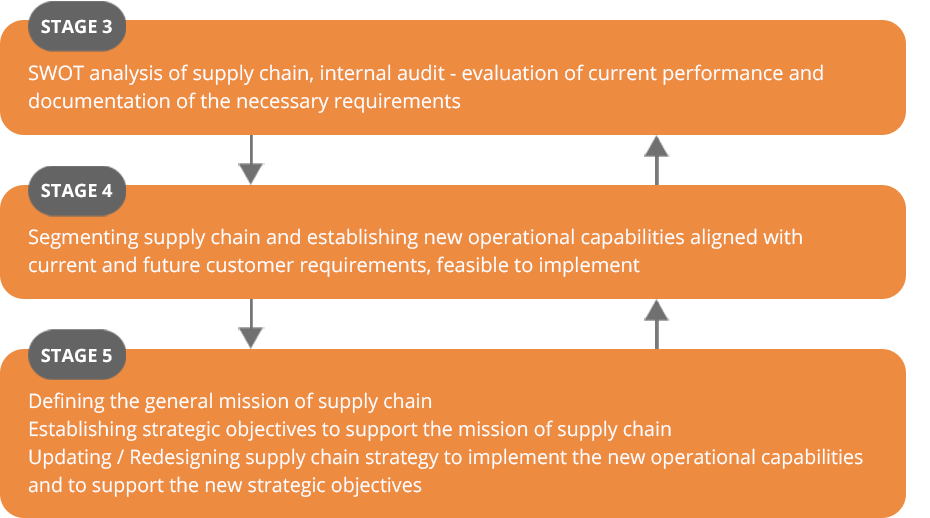
Stages 3, 4 and 5 initiate the process of updating the supply chain strategy to support future business strategy from the following perspectives:
In stages 3, 4, 5, the process of updating supply chain strategy involves the following activities:
- SWOT analysis, supply chain internal audit – evaluation of current performance and documentation of new operational requirements
- Supply Chain segmentation and setting up new operational capabilities in relation to current and future customer requirements, feasible to implement
- Defining the supply chains’s general mission
- Establishing strategic objectives to support supply chain mission
- Update / Redesign supply chain strategy to implement the new operational capacities of logistics chain and support the new strategic objectives
Therefore, the updating supply chain strategy process begins with documenting of new operational requirements for ongoing alignment of departmental and corporate strategies. After documentation of new operational requirements, an audit and SWOT analysis of the company’s supply chain will be carried out to evaluate the operational capabilities in relation to the current and future requirements of the customers.
To define and prioritize new supply chain capabilities or improve existing ones, we suggest creation of an interdepartmental, cross-functional strategy team that includes key people from sales, IT, finance etc. The team will periodically organize work meetings to analyze information related to customer requirements, the competitive values necessary to support the business strategy, the internal capabilities of the supply chain, the modern systems applicable to increase the operational performance, the risks and the resilience of the supply chain.
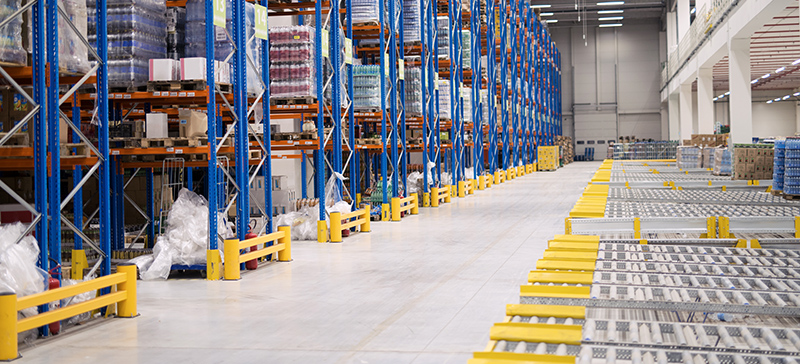
It is recommended to periodically provide information during the strategy development process to the company’s top management, emphasizing the costs but also the benefits that new updates in the supply chain strategy can bring to the company’s financial performance.
During supply chain review process, the following processes will be performed:
- Defining the mission and strategic objectives of the supply chain
- Elaboration of a current list of new capabilities needed by the supply chain and which are financially feasible to implement
- Updating the supply chain strategy for implementation of new operational capacities of supply chain
Note: When updating supply chain strategy, greater importance will be given to strategies of resilience and management of the company’s external risks, accentuated by the Russian-Ukrainian war and the post-Covid-19 pandemic period.
6th stage

Selection and initiation of supply chain strategy implementation projects – in this stage, the following actions will take place:
- Identification of potential strategic projects necessary for implementation of supply chain strategy and drawing up the list of project proposals
- Construction of decision matrix for effective selection of strategic projects from the set of proposal projects . The decision matrix will contain the selection criteria and the weights of importance assigned to each criterion
- Listing the selected projects that will best help to achieve the supply chain strategy
- Initiating the implementation plan of strategic projects
Effective (selected) strategic projects could bring significant functional changes to the supply chain, such as:
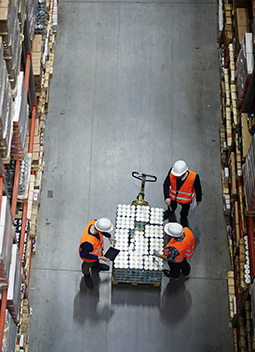
7th stage

The review of organizational structure must be part of implementing process of supply chain strategy. Thus, the changes in the operational structure of the company will include:
The correct modification and establishment of organizational type and structure is of particular importance in implementing supply chain’ competitive strategy.
For example, a prerequisite for an internal supply chain to be agile and flexible is to have an internal organizational structure made up by cross-functional and multidisciplinary process-oriented teams.
In the case of moving from a hierarchical-functional vertical structure to a decentralized horizontal structure, oriented on processes and customer requirements, it could be requested separating some operational teams or merging other teams located in different organizational structures.
The planned integration of a company’s cross-functional processes will lead to reduction of process cycles, increase of end-to-end operational visibility and construction of a supply chain flexible and agile enough to respond quickly to changes in volume and demand mix.
- Strategic level – the people responsible for the development, implementation and monitoring of the supply chain strategy (directors, managers, heads of service etc.)
- Operational level – positions, new or modified roles for the execution of the strategy
When assigning roles and responsibilities to employees, it will be determined if new hires (more people) or layoffs are needed.
Developing new supply chain capabilities and managing them over time will always require new skills and competencies associated with new roles. The strategy team must establish a complete list of skills and competencies required for each position for evaluation and selection of people.
Existing employees will be assessed first, if they already have these skills or if they are capable of acquiring them. Invest in people and collaboration.
In your supply chain network, have employees been able to adapt to new tasks? Do they share and exchange know-how/expertise? Did they work in inter-organizational teams?
Invest in training programs for people’s skills to work efficiently in the company’s internal and external collaborative processes. These collaborative training programs will be essential for the resilience of the company’s supply chain now, but also in the future to be agile and quickly reorganized supply network human resources.
You can also initiate specific plans for digital skills training and advanced analytics for the efficient implementation and management of the new operational capabilities of the supply chain.
8th stage

Reorganizing the new supply chain and associated capabilities requires, along with organizational restructuring, redesign of operational processes and activities, a new set of performance indicators.
You have read Article 2 of the Series “Logistics trends and strategies in 2022”
In the third article, we will present 6 rules for establishing the correct set of KPIs in evaluating supply chain performance.