- Ce este OEE? Ce inseamna OEE?
- Istoria OEE
- Care este diferenta intre Overall Equipment Effectiveness si Overall Equipment Efficiency?
- De ce este important indicatorul OEE?
- Care este diferenta intre OEE, TEEP si OOE?
- Cum se calculeaza OEE?
- Exemplu de calcul OEE
- Beneficii OEE
- Rolul MES in reducerea pierderilor si in cresterea eficientei in productie
OEE - Ce este Overall Equipment Effectiveness si cum se calculeaza? Analiza OEE si importanta ei in productie
Overall Equipment Effectiveness, sau altfel cunoscut ca OEE, este utilizat in companiile din industria producatoare pentru a masura eficacitatea generala a echipamentelor de productie. In urmatoarele randuri vei afla informatii precum ce este OEE si ce beneficii aduce un software OEE (Overall Equipment Effectiveness), care este diferenta dintre Overall Equipment Effectiveness si Overall Equipment Efficiency, cum se calculeaza OEE si cat este de importanta utilizarea acestuia in mediul economic actual, dar si alte detalii de interes. |
Creste productivitatea cu ajutorul OEE
In contextul economic actual, in care costurile cu materiile prime, cu energia si chiar cu resursa umana sunt in continua crestere si au devenit greu de previzionat, imbunatatirea productivitatii si mentinerea unei pozitii competitive in piata pot fi atinse printr-un control sporit asupra modului in care functioneaza echipamentele din productie. Defectarea utiliajelor, blocajele, functionarea echipamentelor la un randament sub cel optim si timpii mari de asteptare reprezinta doar cateva dintre problemele ce pot determina cresterea costurilor de productie, dar si dificultati in respectarea termenelor de livrare a produselor catre clienti.
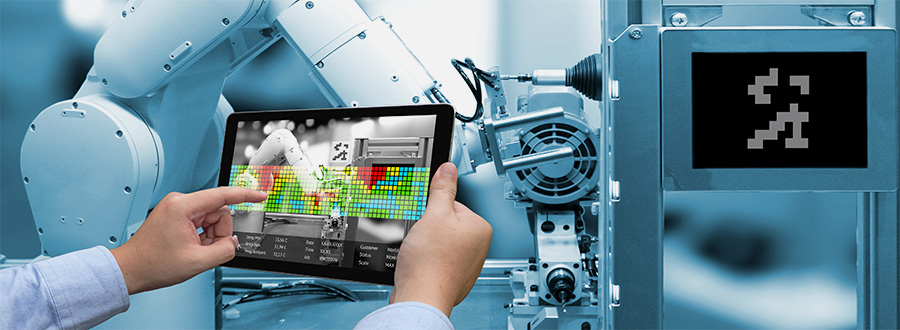
De aceea, intrumentele care permit analiza eficacitatii echipamentelor de productie sunt esentiale atunci cand urmaresti sa minimizezi pierderile si sa produci la costuri cat mai competitive, indiferent de industria in care activezi, iar in acest sens este utila calcularea si urmarirea indicatorului OEE. Prin masurarea eficacitatii utilajelor din fabrica, aspect realizat cu ajutorul indicatorului OEE, companiile au posibilitatea sa identifice si implicit sa diminueze pierderile, crescand astfel productivitatea din zona de productie si intarind pozitia businessului pe piata.
Ce este OEE? Ce inseamna OEE?
OEE este acronimul pentru Overall Equipment Effectiveness, termen englezesc a carui traducere in limba romana inseamna eficacitatea generala sau totala a echipamentului. OEE este indicatorul care masoara cat de bine se realizeaza o operatiune de productie cu echipamentele din fabrica, in comparatie cu potentialul maxim al acestora cu privire la disponibilitate, randament si calitate.
Istoria OEE
Termenul OEE, respectiv Overall Equipment Effectiveness, care inseamna eficacitatea generala a echipamentului, a fost inventat prin anii 1960 de Seiichi Nakajima, pionierul si creatorul japonez al sistemului TPM (Total Productive Maintenance). OEE a fost descris, ca o componenta centrala a metodologiei TPM, in cartea lui Seiichi Nakajima – TPM tenkai (1982, JIPM Tokyo).
Masurarea productivitatii din fabrica cu un software de calcul OEE
Calculul OEE a fost folosit de acesta pentru a calcula cat de eficient este utilizat echipamentul de productie si pentru a demonstra efectele metodei TPM. In prezent, OEE este un standard acceptat la nivel global pentru masurarea productivitatii, iar un OEE ideal sau 100% OEE inseamna ca s-au fabricat doar produse bune, in cel mai scurt timp posibil, fara timpi de oprire.
Care este diferenta intre Overall Equipment Effectiveness si Overall Equipment Efficiency?
Eficacitatea totala a echipamentului de productie si acronimul OEE sunt percepute uneori ca fiind unul si acelasi lucru cu Overall Equipment Efficiency, insa Overall Equipment Effectiveness si Overall Equipment Efficiency prezinta anumite diferente.
De ce este important calculul OEE – Overall Equipment Effectiveness?
OEE este un instrument de masurare relevant pentru toate companiile din industria producatoare, fie ca vorbim de producatorii de alimente / bauturi, de dispozitive medicale sau alte echipamente electronice s.a.m.d. Calculul OEE (Overall Equipment Effectiveness) este o parte indispensabila a strategiei de imbunatatire a activitatilor de productie, impreuna cu TPM (Total Productive Maintenance), ambele fiind instrumente esentiale ale conceptului Lean Manufacturing / Lean Production (care se refera la reducerea risipei din procesul de productie).
Analiza OEE ofera informatii despre ce utilaje / masini / procese necesita imbunatatiri si in ce moment. Utilajele care nu produc la eficienta maxima determina pierderi, iar in lipsa unui calcul al indicatorului OEE, multe pierderi nu pot fi depistate si, prin urmare, nu se pot lua masuri pentru remedierea acestor probleme.
Vizibilitate asupra utilajelor – analiza cu un software de calcul OEE
Asadar, timpul operational al unui utilaj are o importanta cruciala in eficienta inregistrata in productie, deoarece acesta nu poate fi recuperat indiferent de cati operatori sunt disponibili pentru a lucra cu acel utilaj. Altfel spus, datorita unui software de calcul al indicatorului OEE, companiile au vizibilitate asupra tuturor pierderilor de pe fiecare utilaj in parte si pot lua masuri pentru imbunatatirea acestor situatii.
Care este diferenta intre OEE, TEEP si OOE?
OEE, TEEP si OOE sunt termeni frecvent utilizati in industria producatoare, toti reprezentand diferite metode de masurare a diferentei dintre cate bunuri poti teoretic sa produci, fata de cate produci de fapt. Aceasta diferenta te ajuta sa observi unde anume trebuie sa intervii pentru a face imbunatatiri astfel incat sa cresti performantele, fara sa investesti in noi utilaje sau instalatii de productie. Principalii factori care influenteaza OEE, TEEP si OOE sunt: disponibilitatea, calitatea si randamentul.
TEEP – Total Effective Equipment Performance
Este acronimul pentru Total Effective Equipment Performance si ia in considerare toti factorii care influenteaza OEE, insa include si perioadele de timp in care utilajele nu sunt active, fie pentru ca nu sunt functionale, fie pentru ca nu sunt deschise liniile de productie. Un procent de 100% TEEP ar insemna ca masinile din productie sa functioneze 24/7, producand cat mai rapid si fara opriri bunuri de cel mai inalt nivel calitativ.
OOE – Overall Operations Effectivness
Pe de alta parte, este acronimul pentru Overall Operations Effectivness si este o metoda mai putin utilizata de masurare a disponibilitatii liniei de productie. Aceasta prezinta o usoara variatie fata de OEE deoarece face o distinctie intre timpul in care functioneaza fabrica, fata de timpul la care este programat sa ruleze un utilaj.
Spre exemplu, cand se utilizeaza metrica OOE, timpul planificat de intretinere / mentenanta a utilajului este inclus in calculul OOE, insa nu si in calculul OEE. Acest lucru se datoreaza faptului ca, in timpul intretinerii planificate, masina nu este programata sa lucreze. Timpii de schimbare a turelor de lucru reprezinta un alt factor care influenteaza OOE. Cu alte cuvinte, OOE masoara disponibilitatea din punctul in care incepe tura de lucru pana in punctul in care aceasta se termina.
In majoritatea unitatilor de productie, nu este posibil sa incepi si sa finalizezi productia de bunuri astfel incat sa te incadrezi exact in acesti timpi de lucru, deoarece inevitabil vor fi perioade de asteptare. Astfel, masuratoarea OOE in productie cade, de regula, intre TEEP si OEE (timpul total, timpul de functionare, ora programata).
Cum se calculeaza OEE – Overall Equipment Effectiveness?
Calculul OEE cu un software specializat se face pe baza timpului in care este programata masina sa ruleze / lucreze. OEE este de fapt performanta acelei masini in comparatie cu capacitatea sa maxima, adica ceea ce ar putea face utilajul in cauza daca totul ar functiona perfect. Asadar, OEE ia in calcul toate pierderile, iar un scor OEE de 100% inseamna ca produci doar bunuri calitative, cu cea mai mare viteza posibila, fara intreruperi.
Calcularea indicatorului OEE se realizeaza dupa urmatoarea formula de calcul:
OEE = Disponibilitatea x Randamentul x Calitatea
Parametrii folositi in calculul OEE:
Analiza OEE – exemplu de calcul OEE
Pentru o mai buna intelegere asupra calcului eficacitatii generale a echipamentului, vom prezenta un exemplu de calcul OEE si ce imbunatatiri se pot face pentru a creste indicatorul OEE.
Asadar, avand o linie de productie a carei viteza de operare este de 80%, cu 4% rata de productie articole defecte si care ruleaza pe o perioada ce reprezinta 40% din timpul disponibil, ca urmare a intreruperilor cauzate de reglaje si opriri determinate de defectiuni, calculul OEE in acest caz ar fi urmatorul: 40% x 80% x 96%, dupa formula Disponibilitate x Randament x Calitate, caz in care OEE este putin peste 30%.
In aceasta situatie, o imbunatatire semnificativa a scorului OEE s-ar putea obtine in primul rand prin cresterea disponibilitatii de a produce. Prin realizarea unor intretineri proactive si preventive corespunzatoare, care sa permita mentinerea functionalitatii echipamentelor pe o durata cat mai mare de timp, cu cat mai putine blocaje cauzate de defectiunile tehnice, s-ar imbunatati scorul disponibilitatii.
Astfel de masuri permit de regula cresterea semnificativa a scorului privind disponibilitatea. In acest context, sa presupunem ca am obtinut un scor de 90%, caz in care formula de calcul OEE va fi: 90 x 80 x 96, ceea ce inseamna ca indicatorul OEE va fi de aproape 70%.
Un sistem care prezinta un OEE de 85% este considerat a fi de nivel “world class”, iar un exemplu prin care ne-am putea apropia de acest procent ar fi: OEE = 90% (Availability) x 95% (Performance) x 99% (Quality index). Bineinteles, de retinut este ca parametrii de analiza OEE pot varia de la un proces la altul.
Scorul OEE din companii este in general afectat semnificativ de urmatoarele:
Analiza OEE – beneficii
Companiile care folosesc analiza OEE pentru evaluarea nivelului de utilizare a capacitatii unui utilaj sau linii de productie obtin multiple beneficii valoroase, printre cele mai importante observate de catre producatori numarandu-se:
Rolul MES in reducerea pierderilor si in cresterea eficientei in productie
O solutie MES pentru managementul operatiunilor din productie te ajuta, printre altele, sa preiei si sa analizezi usor informatiile de pe utilaje, permitandu-ti sa imbunatatesti eficienta totala a echipamentelor si astfel sa reduci costurile de productie si sa cresti productivitatea. Prin intermediul dashboardului OEE din sistem software MES poti vizualiza usor o serie de informatii cheie (principalele motive de defectiuni ale utilajelor, indicatorul OEE si Top 5 pierderi – pe luna curenta, luna anterioara, intervalul de timp predefinit etc.).
Un soft MES performant permite accesul si la alte tipuri de dashboarduri: dashboard operator, dashboard comenzi de lucru si dashboard utilaj (acesta afiseaza in timp real productia pe utilaj, de la activitati in derulare, viteza curenta, cantiatea produsa / ramasa si pana la timpul ramas si nu numai).